By Bart Borg
KEY TAKEAWAYS:
- Monitor new crop quality promptly
- Identify and monitor risk areas in feed production
- Focus on critical monitoring points for accurate feed quality control.
It’s a good time of year to consider your feed quality assurance program, as we have newly harvested crops in the bin, and processors are producing soybean meal and DDGS using the 2024 crops. A monitoring plan is always good, but it is essential as we begin using the new crop.
Feed quality can be attacked in many ways. Still, I would like to consider what risk areas we have along the continuum, from buying ingredients to formulation, manufacturing, and delivery. Each step has potential problem areas, so monitoring each area helps minimize surprises. It includes a feed of correct nutrient density that includes corn ground to the optimum micron size and is free or low in mycotoxin level. Of course, correct nutrient density needs to include understanding ingredient nutrient content, correct diet formulation, and tight manufacturing processes. Something not right in any of these areas opens the opportunity for the diet not to be accurate and for poor performance to result.
The ingredients listed in Tables 1 and 2 are guides for the basics of ingredient monitoring and specifications. Table 1 indicates the financial impact of a particular quality measure being wrong and, if bad for some time, the entire “pipeline” of pigs has been affected, as well as the severity of the financial consequence of getting it fixed. An excellent example is when phytase levels are low or available phosphorus is low. This would be difficult to see as pigs grow, but it presents a real problem if it is recognized in late finishing that bone strength should be different from what it should be due to underfeeding phosphorus. There is no quick fix to a pig grown on less than adequate phosphorus, and it may be costly due to broken legs, etc.
TABLE 1. Indications of incorrect quality measures and suggestions of cost to recover
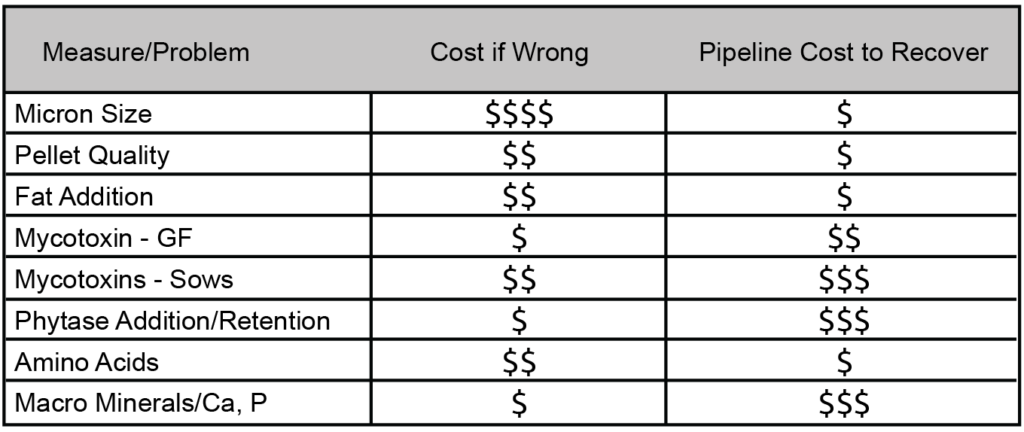
Table 2 provides a closer look at specific ingredients and essential items to be monitored. There are many more minor aspects of ingredient quality to be considered, but these are the ones to ensure you have a handle on. We’ve written articles in the past showing the importance of monitoring the micron size of the corn. Digestibility is reduced, and costs go up when corn micron size is not optimum. Monitoring and understanding if there is a mycotoxin challenge with your area’s crop is essential for corn/grains and DDGS. Remember that even though your corn may not be contaminated, the corn going into an ethanol plant may be, so always keep an eye on DDGS. Figure 1 provides an example of growing pig performance when fed two different sources of DDGS. In this example, there was a quality-related problem with source 1, significantly impacting pig performance.
TABLE 2.
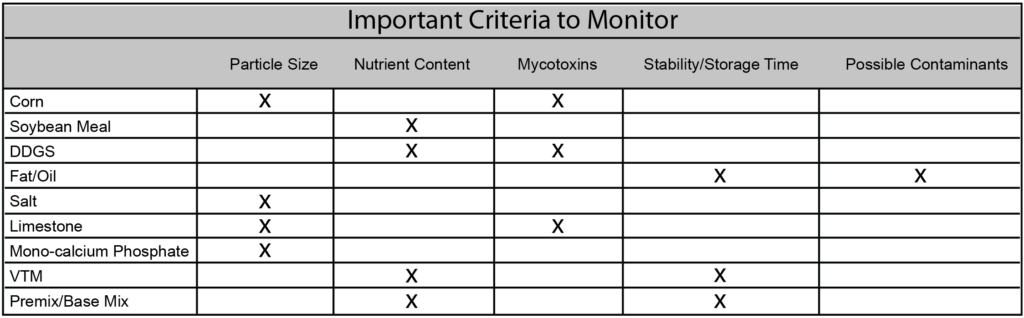
FIGURE 1. Effect of DDG Quality on Average Daily Gain of Growing Pigs
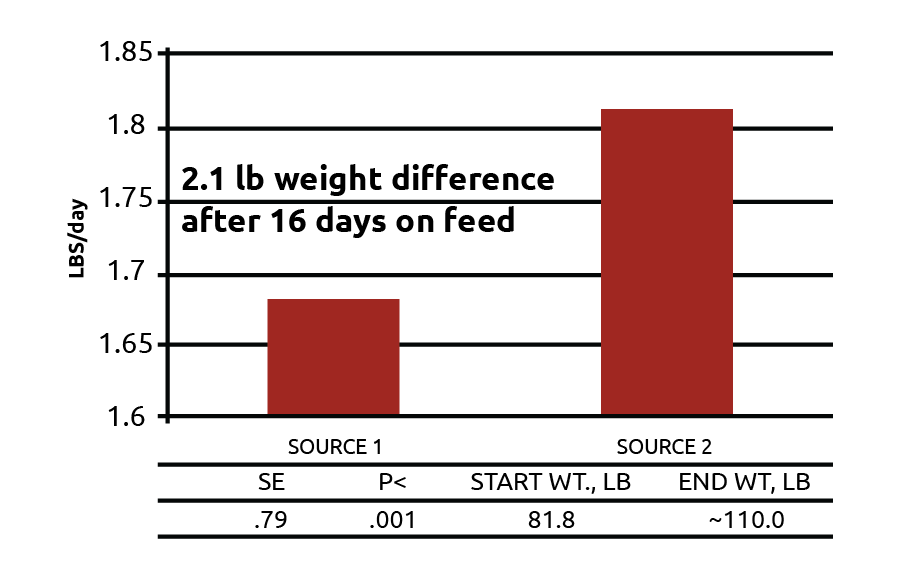
The nutrient content of the crop is also important to pay attention to as we move from one crop year to another. In Figure 2, I’ve graphed the crude protein content of soybean meal from a northern Iowa processing plant. This is an exercise I do every year after we get into the new crop, as the soybean meal protein content will change many times due to the protein content of the soybeans for that crop year. After the baseline gets established, it is usually consistent for the year, but it’s always good to monitor periodically. In this example, you can see the step change in protein content of the soybean meal at the time of harvest when the soy processor begins to bring in new crop beans. Diets should be adjusted as the “new” protein content is understood, so final diets should contain the correct levels of amino acids, etc.
FIGURE 2. Soybean Meal Protein Content Originating from a Common Processing Plant.
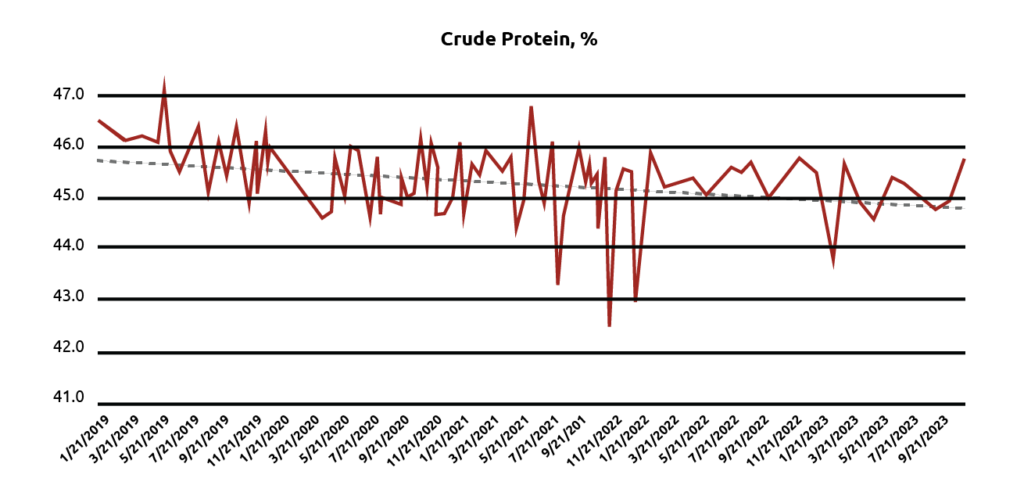
Other items that should be part of a feed quality program include monitoring within the feed manufacturing process. Listed below are must be’s for monitoring of feed quality:
- Mixer tests – at least annually. The coefficient of variation (CV) should be less than 10%
- Testing Buckets for calibration of any liquids (fat/oil) should be done at least each quarter to ensure the mill automation system calibrates the metering device used correctly.
- Ingredient variance reports should be generated from the mill automation system and checked for any ingredient that has a significant variation in the expected amount of the ingredient used compared to the actual.
- Corn micron size monitoring.
If the items listed above are monitored and adjusted accordingly, the diets that are produced and delivered to the pig/turkey are what we expect. However, it’s always good to pull finished feed samples periodically and check the analysis against the expected nutrient content, mycotoxin load, etc. If you have questions or need help gathering some of the information listed above, please contact your Standard Nutrition Services Consultant, and we’ll be happy to help you.